|
Post by mrmotors on Aug 12, 2014 23:37:47 GMT -6
Part of the secondary off the F/A. The sheaves and brake rotor were a bit crusty. The rivet heads were a bit bashed up so I just took it apart. Cleaned up the sheaves and replated them, machined the rotor and got rid of the corrosion and pitting. In the process of rebuilding the chaincase, will put up some more as I go along. Going to rework the bore of the outer helix piece, keyway is stuffed up and it's loose on the shaft. When that's done they will be hard anodized for wear resistance.
|
|
|
Post by mrmotors on Aug 30, 2014 22:05:12 GMT -6
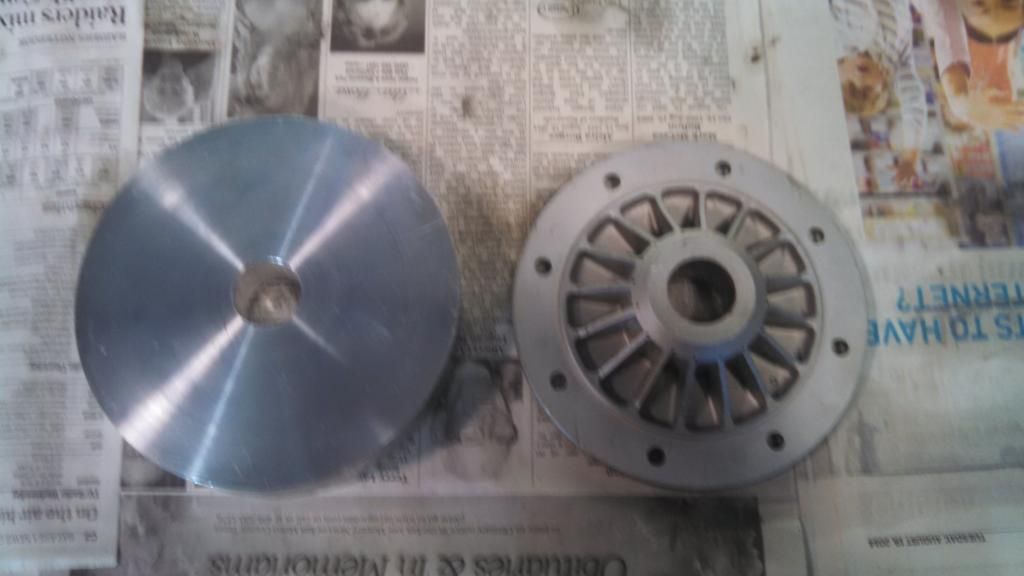 This is the old hub and the lump of aluminum I am making another one from.
|
|
|
Post by mrmotors on Aug 30, 2014 22:06:32 GMT -6
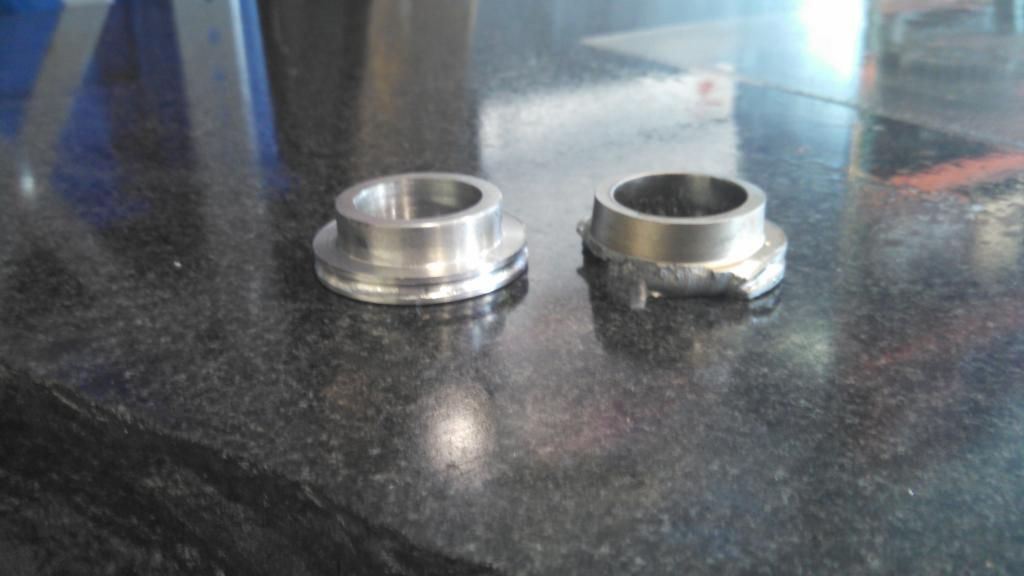 This is the steel spacer piece in the back of the hub that is the chaincase bearing shoulder.
|
|
|
Post by mrmotors on Aug 30, 2014 22:08:02 GMT -6
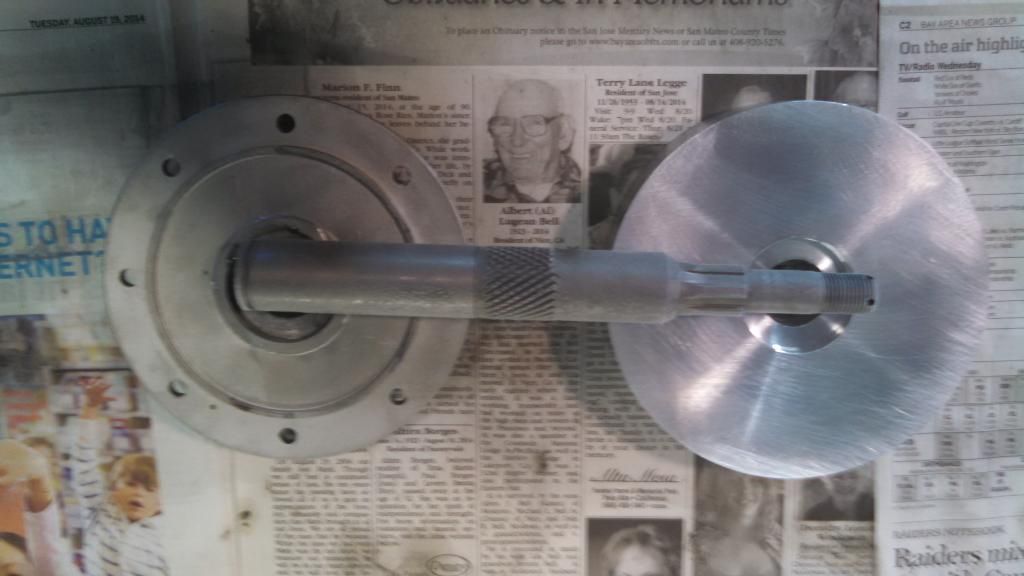 The repaired original shaft, old hub and new un-machined hub piece.
|
|
|
Post by mrmotors on Aug 30, 2014 22:09:06 GMT -6
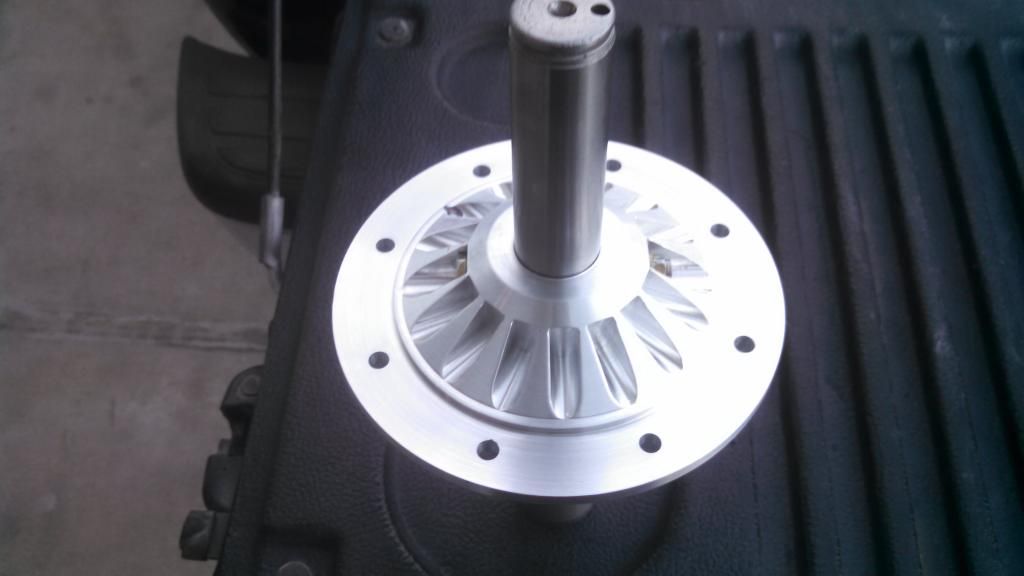 Front, inside face of new hub.
|
|
|
Post by mrmotors on Aug 30, 2014 22:20:13 GMT -6
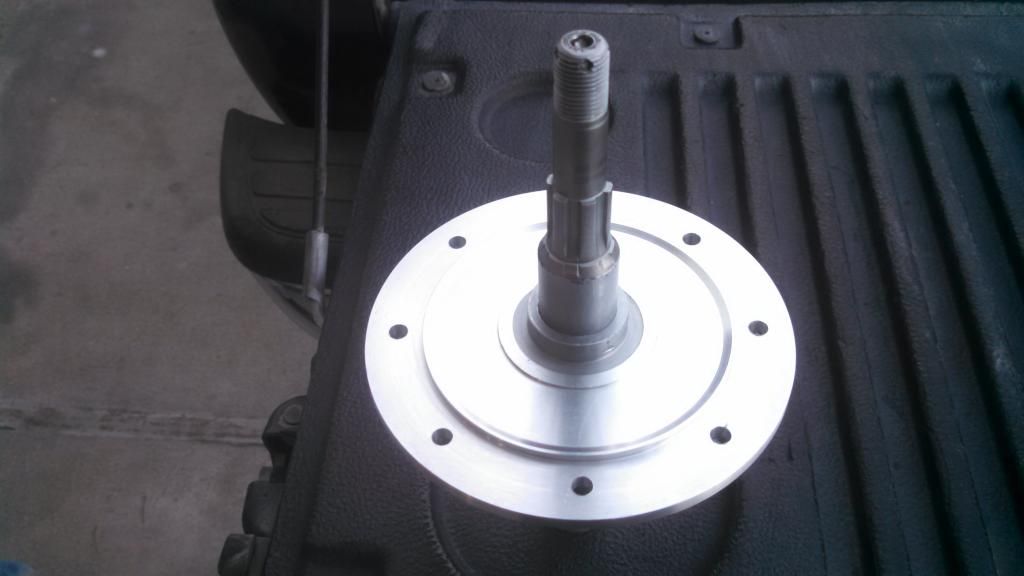 Backside of the new hub. What started all this is that I cleaned up the shaft, which was already undersize and it was then more undersize. I read in the SB's that there should be .002 clearance between the shaft and the helix pieces. Both of these were loose to start with and after cleaning they were really loose, about .012". I had debated trying to repair the bore in the outer helix piece but the keyway was a problem and I couldn't figure a sensible way to deal with it short of making one. I decided to remove the shaft and repair it, as you can see, the removal didn't end quite as anticipated. But, I had the shaft repaired. Ground, metal sprayed and ground to a size that I can bore and fit the bushing in the moveable sheave and the outer helix piece to get the .002 clearance needed. I had a piece of aluminum so I made a new hub. Put the shaft in the freezer over night, heated the aluminum to 450 for an hour and a half and then pressed them together, took about 15 tons force, it had taken a lot of heat and 20 tons to break it loose. I pressed them together before I did all the machining. Got the thing machined, decided to put a cross bolt in it just because it had been apart. Drilled and reamed it, installed an NAS bolt in the hole. Don't think it will spin out---- I will rivet the whole mess back together and have it balanced.
|
|